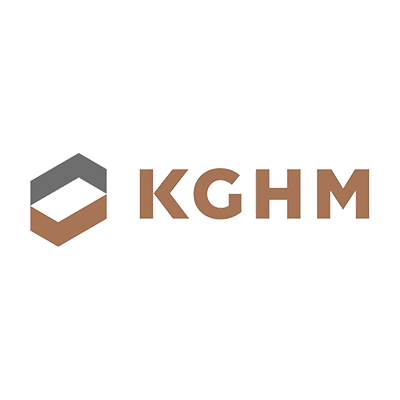
The centralization of purchasing processes supported by IT tools developed on the basis of the Marketplanet Platform allowed one of the largest Polish companies to save approximately 300 million PLN on purchases in the first year.
KGHM Polska Miedź S.A. is the ninth largest copper producer in the world and the second largest producer of silver, employing over 18.5 thousand people, and together with about 30 plants belonging to the Group - over 28 thousand. Such a giant enterprise has obviously very diverse purchase needs, ranging from office supplies to large mining machinery or real estate. Until recently, individual CG Companies pursued independent purchasing policies, resulting in a relatively narrow list of suppliers and the negotiated prices were not necessarily the lowest.
Main challenges in the area of the company's purchases were:
- failure to use the potential for savings in the implementation of purchases,
- decentralisation of purchases - tenders organised by individual plants and units rather than centrally,
- lack of standardization and unification of conducted proceedings,
limited number of suppliers.
- a fixed number of suppliers
- limited fixed number of suppliers.
As in the opinion of the management the purchasing process was inefficient and conducive to abuse, at the end of 2008 a decision was made to implement a new purchasing policy based on the Central Purchasing Office with the support of Marketplanet.
Business benefits:
- 300 million PLN savings achieved in the first 6 months of system operation
- rationalisation of the purchasing organisation by creating a Central Purchasing Office for KGHM
- implementation of a new structure of processes and support for their execution by the IT system
- increase in the quality of collaboration with suppliers
KGHM Polska Miedź S.A. is the ninth largest copper producer in the world and the second largest producer of silver, employing over 18.5 thousand people, and together with about 30 plants belonging to the Group - over 28 thousand. Such a giant enterprise has obviously very diverse purchase needs, ranging from office supplies to large mining machinery or real estate. Until recently, individual CG Companies pursued independent purchasing policies, resulting in a relatively narrow list of suppliers and the negotiated prices were not necessarily the lowest.
Main challenges in the area of the company's purchases were:
- failure to use the potential for savings in the implementation of purchases,
- decentralisation of purchases - tenders organised by individual plants and units rather than centrally,
- lack of standardization and unification of conducted proceedings,
limited number of suppliers.
- a fixed number of suppliers
- limited fixed number of suppliers.
As in the opinion of the management the purchasing process was inefficient and conducive to abuse, at the end of 2008 a decision was made to implement a new purchasing policy based on the Central Purchasing Office with the support of Marketplanet.
Business benefits:
- 300 million PLN savings achieved in the first 6 months of system operation
- rationalisation of the purchasing organisation by creating a Central Purchasing Office for KGHM
- implementation of a new structure of processes and support for their execution by the IT system
- increase in the quality of collaboration with suppliers